Pour les secteurs de l’aéronautique et de l’aviation, les pièces d’usinage qui composent certaines parties mécaniques de leurs engins nécessitent un très haut degré de précision. Cela concerne en particulier les turbines.
Afin de répondre aux exigences du milieu en termes de résistance thermique et physique, il est indispensable que les profilés de ces pièces critiques d’avions et hélicoptères soient conçus par des machines de microérosion, capables de performances inégalées.
Lisez notre article pour connaître les enjeux et les avantages de l’usinage de précision par micro érosion pour les secteurs de l’aéronautique et de l’aviation.
L’usinage de précision des composants des véhicules aériens et nautiques
Depuis plusieurs décennies, l’industrie aéronautique utilise abondamment le micro-usinage par électroérosion pour concevoir les formes particulièrement complexes dans des matériaux difficiles. Il s’agit souvent de métaux soit très résistants et dont la découpe et le perçage nécessitent une technique particulière, soit très précis dont l’usinage requiert une extrême minutie.
Dans tous les cas, les profilés sont calculés au micron près afin d’obtenir les performances et la fiabilité souhaitées, par exemple sur des systèmes de pompes gerotor ou de type chemise-piston. Ils correspondent ainsi parfaitement aux plans tels qu’ils ont été conçus et éprouvés par les ingénieurs spécialisés et leurs bureaux d’études. La société sous-traitante responsable de l’usinage de ces composants métalliques doit donc maîtriser des techniques de pointe qui ne laissent aucune place à l’à peu près. C’est là que la micro érosion entre en jeu.
Exemple : l’importance des micro-trous dans les turbines d’avion
Les micros-trous de refroidissement, appelés communément cooling holes et réalisés dans les aubes de turbines, montrent parfaitement les enjeux des techniques d’usinage de très haute précision par micro-érosion. Les moteurs d’avion sont soumis à des températures extrêmes et ces limites n’ont cessé d’être repoussées avec les progrès de l’industrie aéronautique.
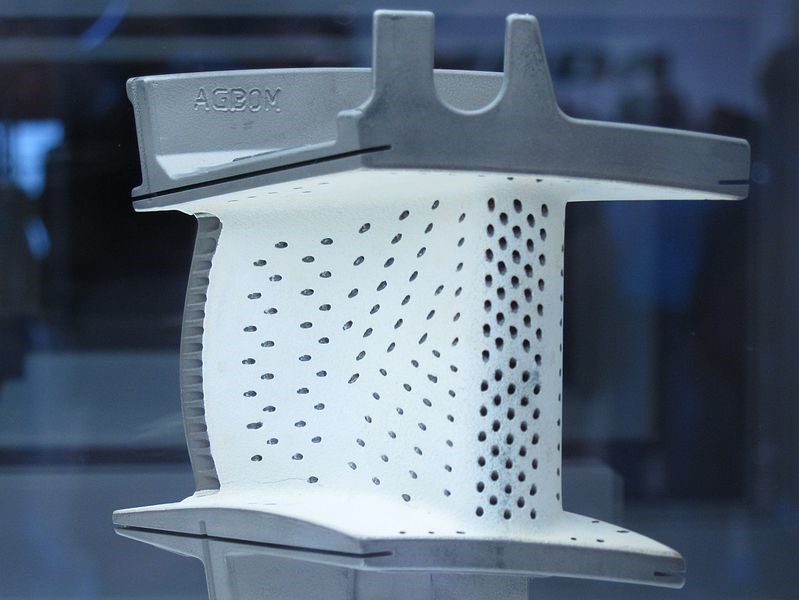
Micro-trous de refroidissement – by O. Cleynen
Un refroidissement possible grâce au micro perçage
Les technologies actuelles de micro-perçage par micro-fraisage permettent le perçage de micro-trous profonds dans les aubes, qui constituent des parties chaudes dans les turbines. Ceux-ci ont généralement un diamètre de l’ordre de quelques dixièmes de millimètre (entre 300 et 500µm). Ils sont indispensables car ils créent une circulation interne d’air, permettant ainsi de dissiper la chaleur de la pièce mécanique.
Le design de l’aube est quant à lui crucial également, tant dans sa forme que dans son surfaçage. Parfois nommé “shape hole”, il joue le rôle de diffuseur avec son profil conique à l’entrée puis cylindrique à l’intérieur, qui favorise fortement le refroidissement. Il contribue aussi à la création d’une fine couche d’air à la surface de la pièce afin d’en améliorer l’isolation thermique. Les micro-trous percés visent à atteindre ces différents objectifs.
Un procédé optimal avec la micro-érosion
La technique optimale pour réaliser ces trous est le micro-perçage par électroérosion, telle que nous la maîtrisons chez Mecasoft. Grâce à ce procédé, nous atteignons un degré de précision, une reproductibilité et une qualité du produit impossibles à atteindre avec un perçage mécanique traditionnel.
Les performances des machines de micro fraisage permettent d’atteindre des hauteurs de perçage de 15mm pour des diamètres de 10µm. Il s’agit donc bien d’un ratio inégalé de 150x. Les états de surface obtenus sont quant à eux excellents avec un Ra < 0.1µm.
Les avantages de la micro érosion dans les secteurs de pointe
Dans les secteurs aussi exigeants que sont ceux de l’aviation civile et plus largement de l’aéronautique (y compris lorsqu’ils sont appliqués au domaine de la défense), l’exactitude d’application et la perfection des produits usinés sont plus que jamais de rigueur. C’est possible grâce au microfraisage et aux différents procédés de micromécanique (découpe, perçage et surfaçage).
Le rendement et la productivité sont également une préoccupation permanente dans l’aéronautique. En utilisant un seul diamètre d’électrode, nous contribuons à l’automatisation de la fabrication des ces aubes monopales.
Le profilage de pièces métalliques complexes
L’EDM est applicable à la production de composants moteurs d’avion, d’hélicoptère ou de véhicule spatial, ainsi qu’aux parties métalliques structurelles, parties de trains d’atterrissage ou encore aux composants d’outillage pour ces secteurs. La technologie EDM permet en outre une application rigoureuse du cahier des charges par l’entreprise de micro-mécanique.
Chez Mecasoft, par exemple, nous sommes en mesure de réaliser tous types de profilés, même les plus complexes (notamment grâce à notre micro-fraiseuse 5 axes) et à partir de tous types de métaux, des plus solides aux plus délicats.
La maîtrise de la reproductibilité
L’un des autres grands avantages de l’EDM est sa parfaite capacité de reproductivité. Grâce à une commande à distance via une interface moderne et sans faille, chaque trou ou chaque élément de relief est strictement identique à tous les autres. Cette reproductibilité s’applique pour une même pièce mais également pour toutes les pièces d’une même série. De cette manière, la qualité des composants finis usinés est constante et homogène.
En conclusion
Chez Mecasoft, nous comptons parmi nos clients des acteurs importants des secteurs aéronautique, spatial et de la défense, comme Airbus, Boeing et Safran ou encore SABCA et SONACA. Notre société de micro-usinage est par ailleurs certifiée EN9100:2018, une norme européenne qui assure à nos clients la qualité exigée par ces secteurs de pointe (aéronautique et aérospatial). Nous réalisons pour ces entreprises des composants métalliques qui leur assurent des produits aérodynamiques, résistants physiquement et thermiquement.
Vous désirez bénéficier de nos services de découpe haute précision ou joindre notre bureau d’études pour vous conseiller dans l’élaboration de votre produit à usiner ? Contactez-nous !