In der Luft- und Raumfahrtindustrie erfordern die Werkstücke, aus denen bestimmte mechanische Teile ihrer Maschinen bestehen, ein sehr hohes Maß an Präzision. Dies gilt insbesondere für Turbinen.
Um den Anforderungen dieses Umfelds hinsichtlich thermischer und physikalischer Belastbarkeit gerecht zu werden, ist es unerlässlich, dass die Profile dieser kritischen Teile von Flugzeugen und Hubschraubern mit Hilfe von Mikroerodiermaschinen gestaltet werden, die zu unübertroffenen Leistungen fähig sind.
Lesen Sie unseren Artikel, um mehr über die Herausforderungen und Vorteile der Präzisionsbearbeitung durch Mikroerosion für die Luft- und Raumfahrtindustrie zu erfahren.
Präzisionsbearbeitung von Bauteilen für Luft- und Wasserfahrzeuge
Bereits seit mehreren Jahrzehnten wird in der Luftfahrtindustrie die Mikrobearbeitung durch Elektroerosion ausgiebig genutzt, um besonders komplexe Formen aus schwierigen Materialien herzustellen. Häufig handelt es sich dabei um Metalle, die sehr widerstandsfähig sind und deren Schneiden und Bohren eine besondere Technik erfordern, oder um sehr präzise Bauteile, deren Bearbeitung mit äußerster Sorgfalt ausgeführt werden muss.
In jedem Fall werden die Profile auf den Mikrometer genau berechnet, um die gewünschte Leistung und Zuverlässigkeit zu erreichen, z. B. bei Gerotor- oder Kolbenmantel-Pumpensystemen. So entsprechen sie exakt den Plänen, wie sie von Fachingenieuren und ihren Planungsbüros entworfen und geprüft wurden. Das Zulieferunternehmen, das für die Bearbeitung dieser Metallbauteile verantwortlich ist, muss daher Spitzentechniken beherrschen, die keinen Raum für Ungenauigkeiten lassen. Hier kommt die Mikroerosion ins Spiel.
Beispiel: Die Bedeutung von Mikrolöchern in Flugzeugturbinen
Die Mikrolöcher für die Kühlung, die allgemein als cooling holes bezeichnet werden und in Turbinenschaufeln angebracht werden, zeigen perfekt die Herausforderungen der hochpräzisen Bearbeitungstechniken durch Mikroerosion. Flugzeugtriebwerke sind extremen Temperaturen ausgesetzt und deren Grenzwerte wurden mit den Fortschritten in der Luftfahrtindustrie immer weiter verschoben.
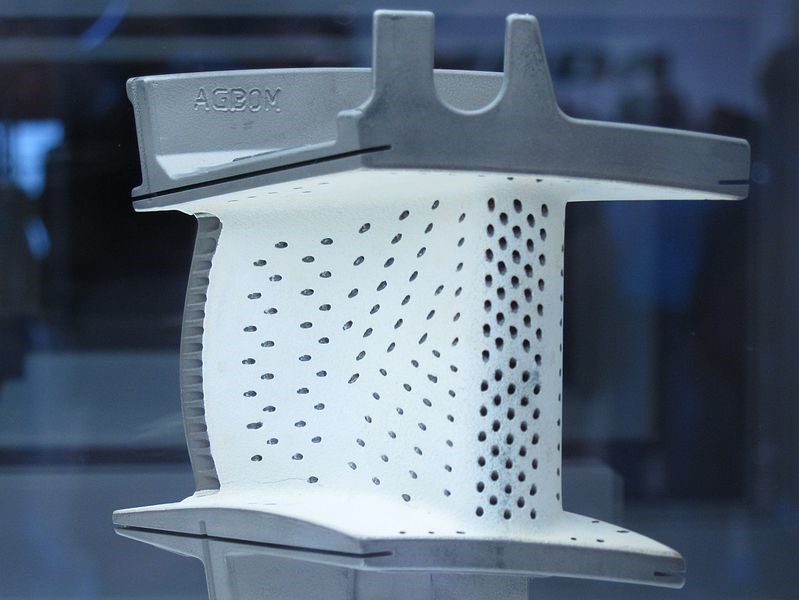
Mikrolöcher zur Kühlung – by O. Cleynen
Kühlung durch Mikrobohrung
Die heutigen Mikrobohrtechnologien ermöglichen das Bohren von tiefen Mikrolöchern in Schaufeln, die als heiße Bauteile in Turbinen eingesetzt werden. Diese haben in der Regel einen Durchmesser in der Größenordnung von einigen Zehntelmillimetern (zwischen 300 und 500 µm). Sie sind unverzichtbar, da sie eine interne Luftzirkulation erzeugen und so die Wärme des mechanischen Teils abführen.
Das Design der Schaufel ist ebenfalls entscheidend, sowohl in Bezug auf die Form als auch auf die Oberflächenbeschaffenheit. Manchmal auch „shape hole“ genannt, fungiert es mit seinem konischen Profil am Eingang und dem anschließenden zylindrischen Profil im Inneren als Diffusor, der die Kühlung stark begünstigt. Außerdem trägt es dazu bei, dass sich an der Oberfläche des Bauteils eine dünne Luftschicht bildet, die die Wärmedämmung verbessert. Mit gebohrten Mikrolöchern sollen diese verschiedenen Ziele erreicht werden.
Ein optimaler Prozess mit Mikroerosion
Die optimale Technik, um diese Löcher zu erzeugen, bietet das Mikrobohren durch Elektroerosion, wie wir es bei Mecasoft beherrschen. Mit diesem Verfahren erreichen wir einen Grad an Genauigkeit, Reproduzierbarkeit und Produktqualität, der mit herkömmlichem mechanischem Bohren nicht möglich ist.
Die Leistungsfähigkeit von Mikrofräsmaschinen ermöglicht Bohrlochhöhen von 15 mm bei Durchmessern von 10 µm. Es handelt sich also um ein unübertroffenes Verhältnis von 150x. Die erzielten Oberflächengüten sind ihrerseits mit einem Ra < 0,1 µm hervorragend.
Vorteile der Mikroerosion in Hightech-Branchen
In so anspruchsvollen Bereichen wie der zivilen Luftfahrt und der Luft- und Raumfahrt im Allgemeinen (auch wenn sie im Verteidigungsbereich angewendet werden) sind die Genauigkeit der Anwendung und die Perfektion der bearbeiteten Produkte mehr denn je unumgänglich. Dies ist dank des Mikrofräsens und der verschiedenen mikromechanischen Verfahren (Schneiden, Bohren und Oberflächenbearbeitung) möglich.
Auch in der Luftfahrt sind Leistung und Produktivität ein ständiges Bestreben. Durch die Verwendung eines einzigen Elektrodendurchmessers tragen wir zur Automatisierung der Herstellung dieser Monoblattschaufeln bei.
Profilieren von komplexen Metallteilen
EDM wird für die Herstellung von Triebwerkskomponenten für Flugzeuge, Hubschrauber oder Raumfahrzeuge sowie für tragende Metallteile, Teile von Fahrwerken oder auch Werkzeugkomponenten für diese Sektoren eingesetzt. Die EDM-Technologie ermöglicht zudem eine exakte Umsetzung der Spezifikationen durch das Mikromechanikunternehmen.
So sind wir bei Mecasoft beispielsweise in der Lage, alle Arten von Profilen herzustellen, selbst die kompliziertesten (vor allem dank unserer 5-achsigen Mikrofräsmaschine) und aus allen Arten von Metallen, von den festesten bis zu den feinsten.
Beherrschung der Reproduzierbarkeit
Ein weiterer großer Vorteil von EDM ist ihre perfekte Reproduzierbarkeit. Dank der Fernsteuerung über eine moderne, nahtlose Schnittstelle sieht jedes Loch oder Reliefelement exakt wie jedes andere aus. Diese Reproduzierbarkeit gilt für ein einzelnes Teil, aber auch für alle Teile einer Serie. Auf diese Weise ist die Qualität der bearbeiteten fertigen Komponenten konstant und einheitlich.
Fazit
Bei Mecasoft zählen wir wichtige Akteure der Luft-, Raumfahrt- und Verteidigungsindustrie zu unseren Kunden – wie Airbus, Boeing und Safran oder SABCA und SONACA. Unser Mikrobearbeitungsunternehmen ist außerdem nach EN 9100:2018 zertifiziert, einer europäischen Norm, die unseren Kunden die Qualität garantiert, die in diesen Hightech-Branchen (Luft- und Raumfahrt) gefordert wird. Wir stellen für diese Unternehmen Metallkomponenten her, die ihnen aerodynamische, physisch und thermisch widerstandsfähige Produkte garantieren.
Möchten Sie unsere Dienstleistungen im Bereich Hochpräzisionsschneiden in Anspruch nehmen oder unsere Entwicklungsabteilung erreichen, um Sie bei der Ausarbeitung Ihres zu bearbeitenden Produkts zu beraten? Kontaktieren Sie uns!