Mecasoft is active in the design of components for various areas of health including those which are particularly demanding. We collaborate in the development of pharmaceutical groups and can assure them of the perfection and traceability of machined parts used in their equipment, mixers and pharmacological microreactors. We are active in the design and production of tools for the pharmaceutical sector, both microfluidic and mesofluidic.
Our engineers will accompany you in the development of your machined components
During your project with Mecasoft, you will work with our team of qualified engineers who are trained in micromechanical techniques. Based on your specification and requirement, we determine the best technique for the manufacture of your microreactor or microfluidic chip. Whether for the composition of a reactor, mixer or polymerisation equipment we validated the design, prototyping and one-off or mass production of the part.
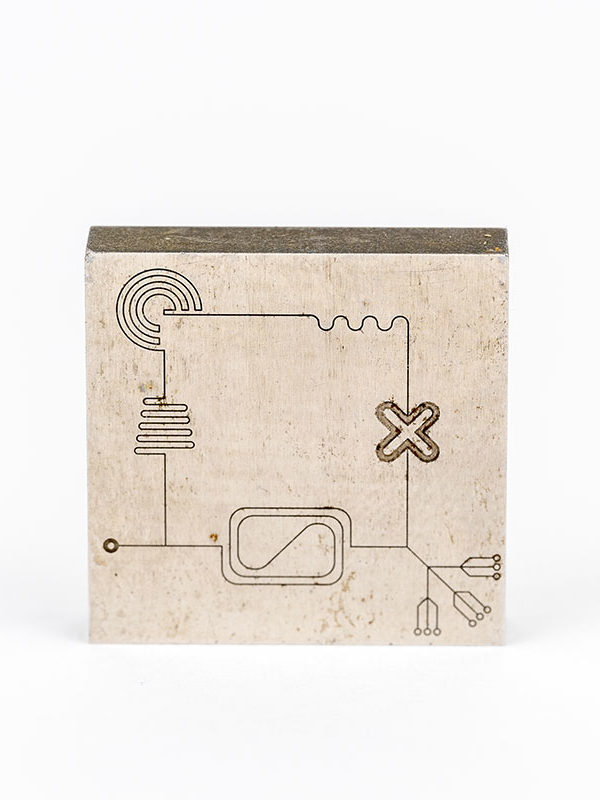
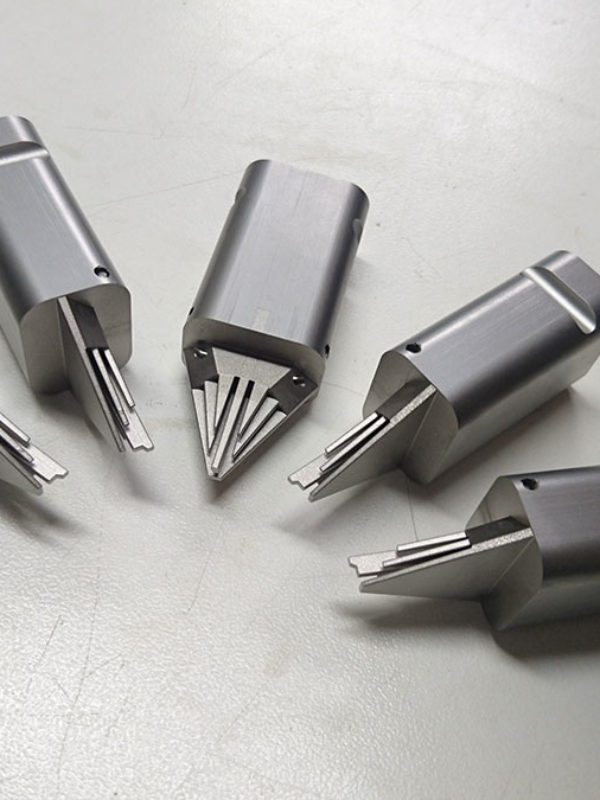
Our proven micromechanics techniques
These proven techniques have been our speciality for over 40 years. Because of this, it is possible to produce complex and 3-dimensional profiles when developing a prototype for the advanced sector of the pharmaceutical industry (and also medical, aeronautical, food, etc.).
Mecasoft has an extensive machine pool that enables us to carry out all types of work requiring the use of micromechanics, down to very demanding diameters of 10 µm to 50 µm. In particular, we work with micro-erosion processes by wire, sinking or drilling, also known a micro-drilling, micro-piercing and micro-cutting. These enable a precision of 1 to 5 µm and surface finishes Ra of 0.05 to 0.1 µm to be achieved.