The medical and hospital sectors require state-of-the-art equipment for treating patients. Of course, to ensure effective results and safety, these components of medical equipment and instruments must have reliable, strong, safe and extremely precise designs.
And a significant proportion of these components demands the use of micro-mechanics in order to achieve the necessary level of precision. This is the case, for example, with certain implantable devices, such as intervertebral implants, or certain prostheses.
We want to tell you more about Mecasoft’s expertise in this field, with a concrete example of an application involving a surgical implant.
Tried and tested technology applied to the world of medicine
Mecasoft boasts some impressive experience in the processing of metal components. Our expertise has its roots in the aerospace industry, for which we have also been certified according to the European standard, EN9100. In particular, we produce complex profiles for aerial and nautical applications.
As a result, we have acquired considerable know-how when it comes to producing ultra-thin elements, whose essential qualities are achieved thanks to micromachining. These elements are used in particular for their flexibility and pliability, which means that their shape can be modified to suit the applications and devices for which they are used.
Machining medical devices: implants and prostheses
Some of the more suitable materials include, for example,316L stainless steel and titanium. The latter is frequently used in the medical and surgical sector for its specific properties: biocompatibility, low mass, strength, low risk of corrosion, radiopacity etc.
Thanks to their particular skills, Mecasoft’s engineers have extended their field of expertise to applications in fields that require the same rigour. Mecasoft produces medical implants and prostheses for orthopaedic use. These devices can be offered both to patients in hospitals and for other uses, such as for veterinary purposes.
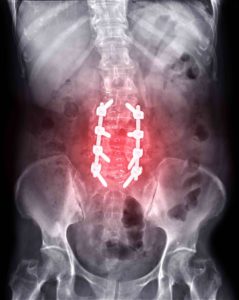
X-ray image of lambosacral spine or L-S spine AP Post operative Fix Lumbar Plates and screw.
As this medical market is constantly expanding, current engineering research means that these implants are improving all the time. High precision machining guarantees a flexible, ultra-thin end product, with a surface roughness of up to Ra < 0.05µm.
Efficacy and safety are always the top priority in medicine, as is confidentiality. Mecasoft is therefore certified in accordance with European EN9100 standards and is in the process of obtaining ISO 13485 certification for Medical Devices. Thanks to its technologies, it focuses in particular on applications such as intervertebral implants, guaranteeing quality for the manufacturer, hospitals and healthcare professionals.
Applications involving intervertebral implants
There are many examples of medical and surgical devices that can be made with the help of micromechanics, including intervertebral implants. Here we would like to explain a concrete application for veterinary use.
Collapsed discs in dogs
Wobbler Syndrome (also known as DACSM or “Disk Associated Cervical Spondylomyelopathy”) is a degenerative condition that affects the spaces between the cervical vertebrae of dogs. It is a condition that is regularly found in large breeds of dogs, but also in small dogs, in particular forms.
These forms consist of instability in the area around one or more intervertebral disc. The discs then tend to get closer together, causing pain and even paralysis in the dog.
Implantable device solution: the IVLS 345 cage
Decompression is therefore required to stabilise the areas in question. The IVLS 345 (Intervertebral Locking System) cage was developed for this purpose. It is available in different sizes to suit the individual morphology of the animal undergoing surgery. With this procedure, the dog regains its mobility and can walk comfortably once again.
In some cases, however, there may still be a risk of a domino effect on the surrounding areas (due to the stiffening that has been induced). To counteract this effect, an improvement has been made to the IVLS 345 cage.
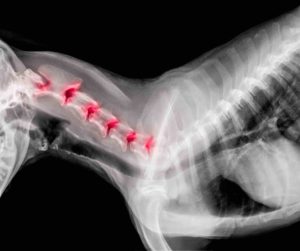
X-ray film of dog lateral view with red highlight in neck joint bone pain areas or cervical disc disease dog- Veterinary medicine- Veterinary anatomy concept
Future-proof solution: the COMFLEX articulated cage
The COMFLEX articulated cage is produced in such a way as to create a joint that allows a few degrees of movement for flexing, extending and twisting. This tolerance helps to reduce the likelihood of an unwanted domino effect by mimicking the characteristics of a real intervertebral disc. A healthy disc can withstand millions of cycles of strain over a lifetime.
This enhancement of the device also means that large dogs can be operated on, whereas the IVLS 345 may have had some limitations and presented a potential risk to the animal.
Find out more about this unique implant
While there are many types of “cage” implants for this purpose, most other solutions are limited in terms of rigidity (increased risk of the famous “domino effect”) or simply long-term resistance. There is currently a high level of confidentiality surrounding the production and distribution of the major advance for the veterinary world outlined above. Further information is available from Mecasoft.