For the aeronautics and aviation sectors, the machined parts that make up some mechanical components of their engines or actuators require a very high degree of precision. This applies to turbines in particular.
In order to meet the requirements of the environment in terms of thermal and physical resistance, it is essential that the profiles of these critical aircraft and helicopter parts are designed by micro-erosion machines, capable of unparalleled performance.
Read our article to learn about the solutions and benefits offered by precision micro-erosion machining for the aeronautics and aviation industries.
Precision machining of aircraft and watercraft components
For several decades, the aeronautical industry has made extensive use of EDM micro-machining to design particularly complex shapes in difficult materials. These are often very strong metals that require a special technique for cutting and drilling, or very particular metals that need to be machined with extreme care.
In all cases, the profiles are calculated to the nearest micron to achieve the desired performance and reliability, for instance in gerotor or sleeve-piston pump systems. In doing so, they are perfectly in line with the plans designed and tested by specialist engineers and their engineering consultancy agencies. As such, the sub-contracting company responsible for the machining of these metal components needs to master state-of-the-art techniques that leave no room for improvisation. This is where micro-erosion comes in.
Example: the importance of micro-holes in aircraft turbines
Micro-cooling holes, commonly known as cooling holes and made in turbine blades, are a perfect example of the challenges of high precision micro-erosion machining techniques. Aircraft engines are subject to extreme temperatures and these limits have consistently been stretched further and further as the aeronautical industry advanced.
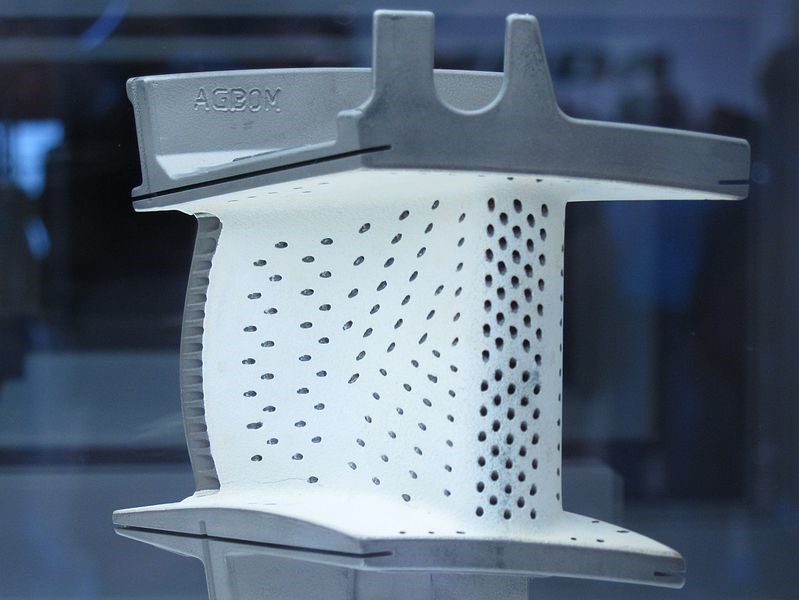
Micro-holes for cooling – by O. Cleynen
Cooling is made possible thanks to micro-drilling
Current micro-milling technologies allow deep micro-holes to be drilled in the blades, which are the hot parts in the turbines. These are generally a few tenths of a millimetre in diameter (between 300 and 500 µm). The holes are crucial because they create internal air circulation, thereby dissipating the heat from the mechanical part.
The design of the blade is also critical both in terms of shape and surface. Sometimes called a “shape hole”, it acts as a diffuser with its conical profile at the entrance and cylindrical profile inside, which is highly conducive to cooling. It also helps to create a thin layer of air on the surface of the part to improve thermal insulation. The micro-holes are designed to achieve these various goals.
Optimum process with micro-erosion
The optimum technique for making these holes is micro EDM drilling, which Mecasoft fully masters. With this process, we achieve a degree of precision, reproducibility and product quality that would be impossible to achieve with traditional mechanical drilling.
The performance of micro-milling machines allows for drilling heights of 15 mm for diameters of 10 µm. This is an unparalleled ratio of 150x. The surface finishes obtained are excellent with an Ra < 0.1 µm.
The benefits of micro-erosion in high-tech sectors
In the particularly demanding the civil aviation and, more broadly, aeronautics industries (including defence) the accuracy of application and the perfection of machined products are more important than ever. This is made possible thanks to micro-milling and various micromechanical processes (cutting, drilling and surfacing).
Efficiency and productivity are also a constant concern in the aeronautical industry. By using a single electrode diameter, we are helping to automate the manufacturing of these single-blade vanes.
Profiling of complex metal parts
EDM can be used in the production of aircraft, helicopter and spacecraft engine components, as well as structural metal parts, landing gear parts and tooling components for these sectors. The EDM technology also allows micro-mechanics companies to rigorously apply the specifications.
Mecasoft is capable of producing all types of profiles, even the most complex ones (thanks to our 5-axis micro-milling machine) and from all types of metal, from the most solid to the most delicate.
Proficient at ensuring reproducibility
Another major advantage of the EDM is its perfect reproducibility. Thanks to remote control via a flawless modern interface, each hole or relief element is exactly the same as all the others. This reproducibility applies not only to a single part but also to all parts in the same series. In doing so, we are able to ensure the consistency and homogeneity of the quality of the finished machined components.
In conclusion
Mecasoft’s map of customers includes major players in the aeronautics, space and defence industries, such as Airbus, Boeing and Safran, SABCA and SONACA. What is more, our micro-machining company is EN9100:2018-certified. EN9100:2018 is a European standard that allows our customers to rest safe in the knowledge they are getting the quality required by these high-tech sectors (aeronautics and aerospace). We produce metal components for these companies to ensure aerodynamic, physically and thermally resistant products.
Interested in benefiting from our high-precision cutting services or get in touch with our design engineering department to advise you on the development of your product to be machined? Contact us!