De bewerkte onderdelen waaruit bepaalde mechanische onderdelen van machines in de lucht- en ruimtevaartsector bestaan, vereisen een zeer grote precisie. Dit geldt met name voor turbines.
Om te kunnen voldoen aan de omgevingsvereisten op het gebied van thermische en fysieke weerstand, moeten de profielen van deze kritieke vliegtuig- en helikopteronderdelen worden gemaakt met micro-erosiemachines die ongeëvenaarde prestaties kunnen leveren.
Lees ons artikel over de uitdagingen en voordelen van precisiebewerking door micro-erosie voor de lucht- en ruimtevaartsector.
Precisiebewerking van onderdelen voor lucht- en watervoertuigen
De lucht- en ruimtevaartindustrie maakt al decennia intensief gebruik van microbewerking door elektro-erosie om bijzonder complexe vormen in moeilijke materialen te maken. Vaak gaat het om zeer sterke metalen die een speciale snij- en boortechniek vereisen, of die heel specifiek zijn en met uiterste zorg moeten worden bewerkt.
De profielen worden altijd tot op de micron nauwkeurig berekend om te komen tot de gewenste prestaties en betrouwbaarheid, bijvoorbeeld in gerotorpompen of pompsystemen met zuigerbus. Zo komen ze dus perfect overeen met de plannen zoals ze zijn ontworpen en getest door de gespecialiseerde ingenieurs en hun studiebureaus. Het toeleveringsbedrijf dat verantwoordelijk is voor de bewerking van deze metalen onderdelen moet dus de modernste technieken beheersen die geen ruimte laten voor improvisatie. En hier wordt micro-erosie belangrijk.
Voorbeeld: het belang van microgaten in vliegtuigturbines
De microkoelgaten in turbinebladen, algemeen bekend als cooling holes, zijn een perfect voorbeeld van het belang van hogeprecisiebewerkingen door micro-erosie. Vliegtuigmotoren zijn onderhevig aan extreme temperaturen en deze grenzen werden steeds verder verlegd naarmate de lucht- en ruimtevaartsector verder ontwikkelde.
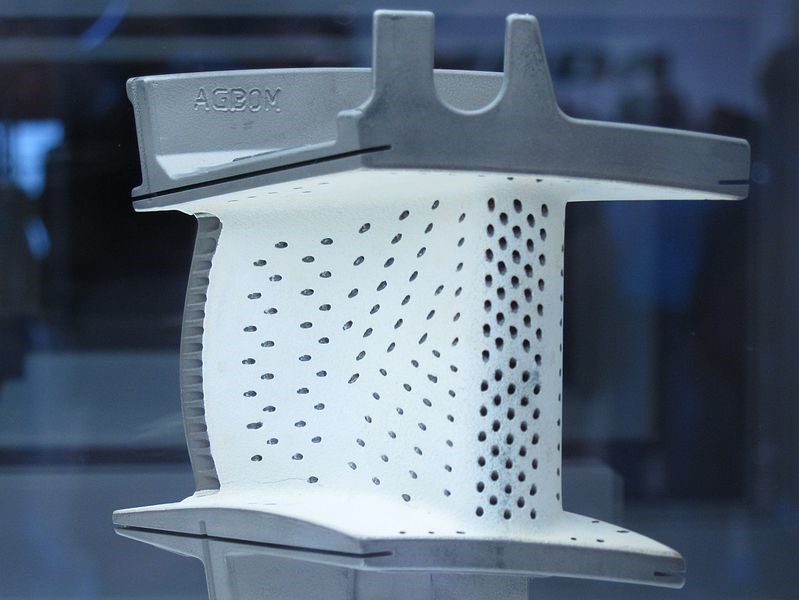
Micro koelgaten – by O. Cleynen
Koeling is mogelijk dankzij microboringen
Met de huidige technologieën voor microdoorboringen door microfrezen kunnen we diepe micro-gaten boren in de bladen, die de warme onderdelen van de turbines zijn. Doorgaans hebben deze doorboringen een diameter van enkele tienden van een millimeter (tussen 300 en 500 µm). Ze zijn van essentieel belang omdat ze zorgen voor een interne luchtcirculatie, waardoor de warmte van het mechanische onderdeel wordt afgevoerd.
Ook het ontwerp van het blad is van cruciaal belang, zowel wat de vorm als het oppervlak betreft. Het wordt soms ook “shape hole” genoemd, omdat het ter hoogte van de ingang een conisch profiel heeft en binnenin cilindrische profiel; daardoor werkt het als een verspreider, wat de koeling sterk bevordert. Het helpt ook om een dunne luchtlaag te creëren op het oppervlak van het onderdeel om de thermische isolatie ervan te verbeteren. De microgaten zijn ontworpen om deze verschillende doelstellingen te bereiken.
Een optimaal proces met micro-erosie
De optimale techniek om deze gaten te maken is microdoorboring door elektro-erosie en deze techniek beheersen wij bij Mecasoft. Met dit proces bereiken wij een mate van precisie, reproduceerbaarheid en productkwaliteit die met traditioneel mechanisch boren onmogelijk te bereiken zou zijn.
Dankzij de prestaties van microfreesmachines zijn boorhoogten van 15 mm mogelijk voor diameters van 10 µm. Dit is een ongeëvenaarde verhouding van 150x. De verkregen oppervlakteafwerking is uitstekend met een Ra < 0,1 µm.
De voordelen van micro-erosie in geavanceerde sectoren
In sectoren die zo veeleisend zijn als de burgerluchtvaart en de luchtvaart in het algemeen (inclusief defensie) zijn de nauwkeurigheid van de toepassing en de perfectie van de bewerkte producten belangrijker dan ooit. Dit kan verwezenlijkt worden dankzij microfrezen en de verschillende micromechanische processen (snijden, boren en oppervlaktebehandeling).
Rendement en productiviteit zijn ook een constante zorg in de lucht- en ruimtevaartindustrie. Door een enkele elektrodediameter te gebruiken, helpen wij de productie van deze enkelvoudige bladen te automatiseren.
Het profileren van complexe metalen onderdelen
EDM wordt gebruikt voor de productie van motoronderdelen voor vliegtuigen, helikopters en ruimtevaartuigen, en ook van structurele metalen onderdelen, onderdelen van landingsgestellen en gereedschapsonderdelen voor deze sectoren. Dankzij de EDM-technologie kan het micromechanisch bedrijf het bestek nauwgezet volgen.
Bij Mecasoft kunnen we bijvoorbeeld alle soorten profielen produceren, zelfs de meest complexe (dankzij onze 5-assige microfreesmachine), uit alle soorten metaal, van het sterkste tot het delicaatste.
Beheersing van de reproduceerbaarheid
Nog een groot voordeel van EDM is de perfecte reproduceerbaarheid. Dankzij de afstandsbediening via een moderne, naadloze interface is elk gat of reliëfelement precies hetzelfde als alle andere. Deze reproduceerbaarheid geldt niet alleen voor eenzelfde onderdeel, maar ook voor alle onderdelen van eenzelfde reeks. Zo is de kwaliteit van de bewerkte onderdelen constant en homogeen.
Conclusie
Enkele van de klanten van Mecasoft zijn grote spelers in de sectoren van de lucht- en ruimtevaart en defensie, zoals Airbus, Boeing en Safran, maar ook SABCA en SONACA. Ons microbewerkingsbedrijf heeft ook het certificaat EN9100:2018, een Europese norm die onze klanten verzekert van de kwaliteit die deze geavanceerde sectoren (lucht- en ruimtevaart) vereisen. Wij produceren metalen onderdelen voor deze bedrijven die gegarandeerd aerodynamisch en fysiek en thermisch resistent zijn.
Wilt u een beroep doen op onze diensten voor heet uiterst nauwkeurig uitsnijden of wenst u in contact te komen met ons studiebureau om u te adviseren over de ontwikkeling van uw te bewerken product? Neem contact met ons op!